Zrozumienie natury laków
Laki atakują turbiny od wewnątrz, niszczą wydajność i stanowią zagrożenie dla działalności. Jednak aby z nimi wygrać, trzeba je najpierw zrozumieć.
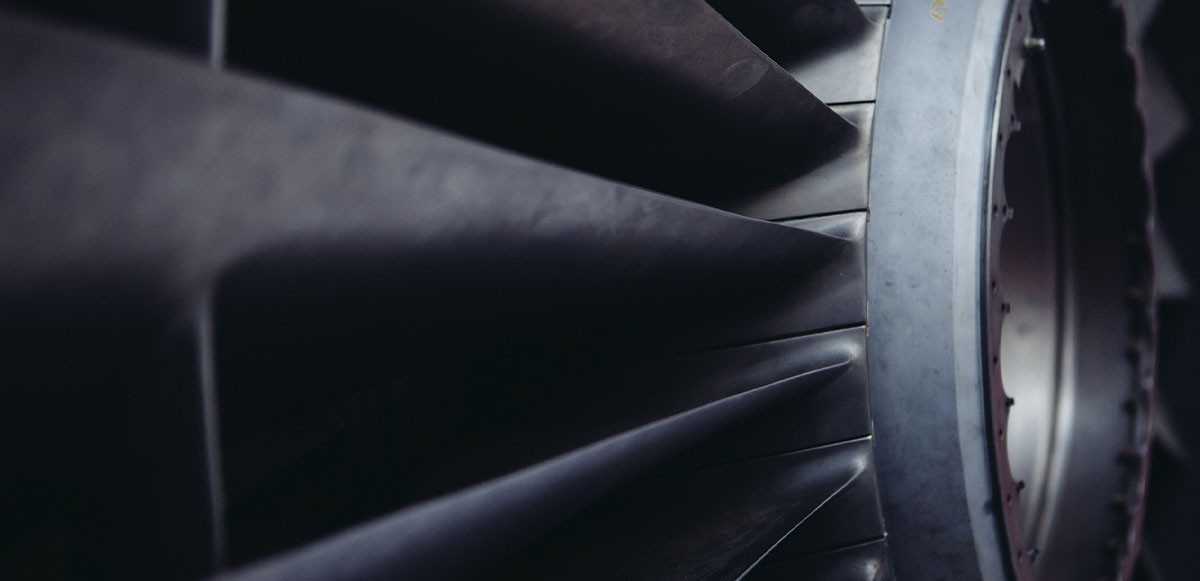
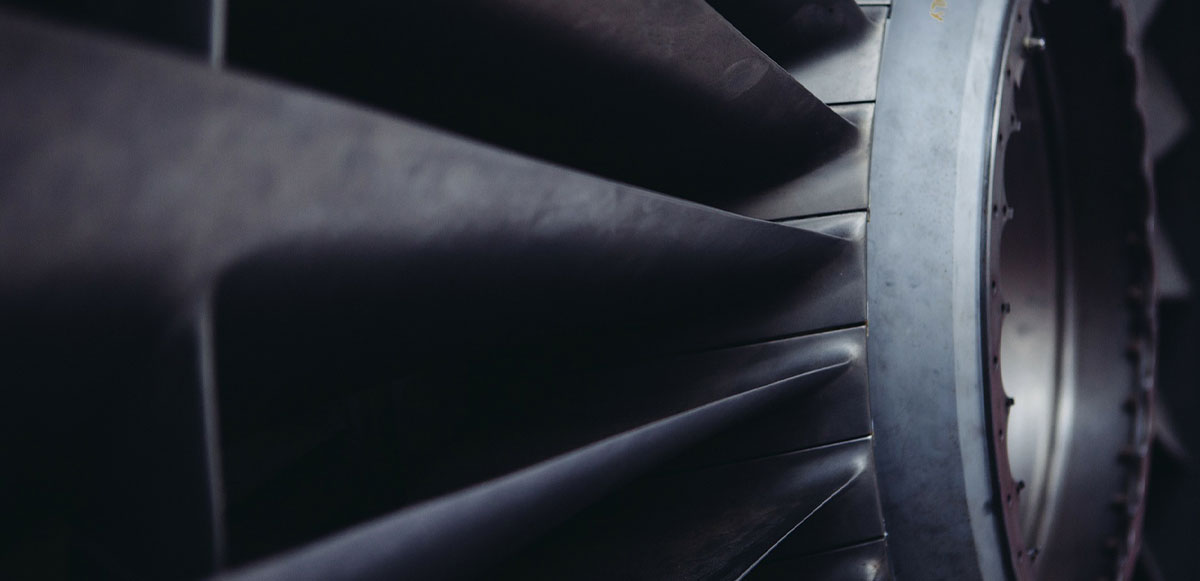
Laki stanowią częsty problem w układach obiegowych, w których zapewniony jest stały dopływ oleju do łożysk, przekładni i innych elementów maszyn przemysłowych. Nawet najmniejsze ilości laków mogą ograniczać wydajność układu i powodować awarie. Szlam lub lak gromadzące się na serwozaworach lub zaworach termostatycznych mogą powodować ich blokowanie, przegrzewanie się łożysk i słabą wymianę cieplną, nierzadko skutkując wzrostem temperatury oleju. Stałe cząstki zanieczyszczeń osadzające się w formie laków mogą także powodować wzrost zużycia podzespołów w zaworach, przekładniach i łożyskach.
Laki nagromadzone w układach turbin mogą wpływać w bardzo negatywny sposób na wydajność układu, trwałość użytkową urządzeń, elastyczność działań i trwałość oleju. W całym okresie użytkowania urządzenia może to powodować ogromne straty finansowe.
Każdy z tych czynników może spowodować degradację oleju, co wpływa na powstawanie prekursorów laków, tworzących z czasem kolejne warstwy laku. Powstałe laki są cienkim, nierozpuszczalnym w oleju osadem złożonym w głównej mierze z cząstek organicznych w połączeniu z metalami, solami nieorganicznymi i innymi zanieczyszczeniami, których nie da się łatwo usunąć suchą, miękką ścierką. Tworzy się powłoka przywierająca do wewnętrznych powierzchni, która może mieć różną postać – od lepkiej po twardą – a także różne kolory: szary, brązowy, bursztynowy.
Choć poniższa lista nie jest ostateczna, przedstawiamy symptomy mogące świadczyć o obecności laków: wadliwa praca podzespołu, w tym blokowanie zaworów i siłowników hydraulicznych, subsynchroniczne drgania łożysk o dużej prędkości i uszczelnień, zmniejszony dopływ oleju lub zwiększona częstotliwość wymiany filtrów.
Ostrzeżeniem jest również często temperatura układu, w którym uruchamiają się alarmy informujące o jej wzroście, wyższa temperatura łożyska głównego lub komory i słaba wymiana ciepła w chłodnicy oleju, prowadzące do ogólnej wysokiej temperatury oleju lub obniżania parametrów pracy maszyn dla utrzymania temperatur poniżej wartości alarmowych.I wreszcie stan samego oleju – ciemnienie, nieprzyjemny zapach, wzrost liczby kwasowej, wzrost lepkości, ślady osadów i/lub szlamu, zwiększona liczba cząstek stałych, wysoki wskaźnik MPC (badanie kolometryczne membrany) i szybki spadek trwałości oleju na skutek utleniania – wszystkie te czynniki wskazują na problemy układu.
Dodatkowo wszystkie badania analizy oleju stosowane do wykrywania problemów z lakami wiążą się z pewnymi wyzwaniami:
- Testowane próbki oleju mogą nie być reprezentatywne dla oleju w całym układzie
- Tendencja do tworzenia laków może się zmieniać w ciągu roku, w zależności od stopnia wykorzystania układu – produkty degradacji często wytrącają się, tworząc osad, w trakcie przestojów
- Prekursory laków trudno jest mierzyć, ponieważ (a) są bardzo małe (czasami < 0,1 μm) i (b) metodologie badań uwzględniają jedynie miękkie prekursory laku w zawiesinie, jednak prekursory rozpuszczają się w oleju i w zależności od postępowania z próbką mogą być zawarte w zawiesinie lub nie
- Dla określenia predyspozycji do powstania laków, a zarazem predyspozycji do ich osadzania się, testy mierzą ogólną „kondycję” oleju i pakietu dodatków uszlachetniających bądź ilość prekursorów laków w oleju
Nie ma bezpośredniego, ostatecznego sposobu weryfikacji problemów układu związanych z obecnością laków, który nie wymagałby pomiaru najważniejszych parametrów, takich jak histereza zaworu lub skuteczność pracy chłodnicy oleju czy też demontażu układu dla wizualnego określenia przyczyny.
Nathan Knotts, pracujący jako Portfolio Architect for Industrial Products, wyjaśnia: „Technologia VARTECH powstała w efekcie naszych badań skoncentrowanych na produktach obecnych na rynku i ich skuteczności. Przyjrzeliśmy się najważniejszym obszarom, takim jak wykorzystanie rozpuszczalników w środkach czyszczących. Choć pomagają one w usuwaniu laków, obniżają także temperaturę zapłonu, co może prowadzić do większej liczby spalin czy większych ograniczeń temperaturowych, a także stwarza ryzyko pożaru czy wybuchu.
Knotts kontynuuje: „Analiza danych z badań laboratoryjnych i testów eksploatacyjnych Texaco VARTECH Industrial System Cleaner wykazała wiele korzyści w stosunku do konwencjonalnych środków czyszczących, co jest owocem naszych starań o wprowadzenie systemu, który czyściłby skutecznie, nie stwarzając przy tym ograniczeń dla działania maszyn. Po pierwsze, VARTECH jest kompatybilny z wieloma stosowanymi obecnie olejami w zalecanym stężeniu 5 - 20% objętości i przez zalecany czas (co pozwala na jego dłuższe pozostawienie w układzie i zasadniczo eliminuje potrzebę przepłukiwania). Wykazano także, że środek pomaga ograniczać blokowanie filtrów i przyczynia się do skutecznego usuwania osadów, a przy tym pomaga rozpuszczać laki osadzone na powierzchniach wewnętrznych, ułatwiając ich stabilizację do czasu usunięcia wraz ze zużytym olejem. I wreszcie charakteryzuje się lepkością 53 cSt, dzięki czemu jest skuteczny w przypadku oleju o lepkości zgodnej z ISO 32-68, nie wpływając na nią znacząco w zalecanych stężeniach. Ma przy tym minimalny wpływ na oddzielanie wody od oleju i na długoterminową wydajność nowego oleju, o ile jego pozostałości w tym oleju nie przekroczą 2%.”
Tak było w przypadku jednego z pierwszych testów VARTECH w USA. Obsługa turbin gazowych w środowisku o wymagającym klimacie, jakim jest Dolina Kalifornijska z panującymi tam wysokimi temperaturami (zazwyczaj między 30º a 40ºC), musi stwarzać dodatkowe przeszkody. Oddział San Joaquin Valley (SJV) firmy Chevron obsługuje ponad 16 000 szybów, wydobywając 159 000 baryłek ropy i 53 miliony stóp sześciennych gazu ziemnego dziennie. SJV dysponuje światowej klasy wiedzą ekspercką dotyczącą wydobycia gęstej ropy naftowej przy wykorzystaniu pary wodnej, przy jednoczesnym wytwarzaniu pary i energii elektrycznej. Para ułatwia wydobycie ropy przy wykorzystaniu specjalnego procesu zalewania parą wodną, natomiast elektryczność jest sprzedawana zakładowi energetycznemu. W okresie letnim łożyska turbiny gazowej nagrzewały się zbyt silnie, by umożliwiać pracę z pełną wydajnością, przez co turbina mogła wytwarzać zaledwie 3,3 MW energii, znacznie poniżej swoich możliwości wynoszących 5,5 MW. Wysokie temperatury otoczenia były częściowo odpowiedzialne za problem, jednak zespół podejrzewał, że na skuteczność chłodnic oleju wpływają także laki, co zostało potwierdzone po kontroli.
Aby zaradzić temu problemowi, zespół Texaco VARTECH pod przewodnictwem Paula Sly zajmującego stanowisko Global Industrial OEM Specialist, zastąpił 15% używanego oleju środkiem Texaco VARTECH Industrial System Cleaner, uruchamiając następnie układ na nowo. Kiedy turbina gazowa zbliżała się do swojej pełnej wydajności, widać było, że nastąpiła radykalna zmiana. Wszystkie temperatury układu mieściły się w akceptowalnych zakresach, nie uruchamiając żadnych alarmów. Turbina gazowa pracowała dalej z pełną mocą przez dwa tygodnie, bez alarmów dotyczących wysokich temperatur, po czym spuszczono z układu mieszaninę zużytego oleju turbinowego i VARTECH Industrial System Cleaner. Układ został przepłukany, wymieniono filtry i wlano do środka olej turbinowy Texaco GST. W efekcie SJV może eksploatować swoje systemy kogeneracyjne z pełną wydajnością przez cały rok, niezależnie od temperatury otoczenia, zyskując ponad 350 000 dolarów rocznego zysku, jaki wcześniej utracono.
Kolejna okazja do przetestowania technologii VARTECH nadarzyła się na jednym z największych pól naftowych w Zatoce Meksykańskiej. Utrata produkcji energii jest zawsze kosztowna i należy jej unikać, na ile to możliwe. Jednak kiedy chodzi o energię zasilającą platformę wiertniczą typu spar, osadzoną na głębokości 4 100 stóp w odległości 190 mil od amerykańskiego wybrzeża, jej brak oznacza zawieszenie całej działalności. Kiedy produkcję ropy utrudniały komory oleju w zestawach generatorów, które stale się nagrzewały, uruchamiając alarmy ostrzegawcze, nowa technologia VARTECH marki Texaco okazała się nieodzowna dla zapewnienia długotrwałego rozwiązania. Wykorzystanie technologii VARTECH nie tylko pomogło klientowi oszczędzić nawet 81 000 dolarów kosztów konserwacji, ale przyczyniło się także do poprawy bezpieczeństwa i obniżyło ryzyko dla środowiska, dzięki brakowi konieczności wymiany sprzętu. 12 miesięcy po pierwszym użyciu technologii VARTECH na platformie typu spar na Tahiti, nie odnotowano alarmów związanych z wysoką temperaturą, a zatem nie było także przedwczesnych wyłączeń systemu.
Paul Sly, Global Industrial OEM Specialist, podsumowuje: „Wszyscy zdajemy sobie sprawę z faktu, że utrata zysków spowodowana przez nieplanowane lub dłuższe niż się spodziewano przestoje może być ogromna. Wyzwaniem było dla nas stworzenie rozwiązania, w którym odeszlibyśmy od polegania na filtracji laków i starych metodach ich usuwania. Zastosowanie dwuetapowego programu VARTECH, w połączeniu z naszym monitorowaniem oleju LubeWatch, spowodowało udaną zmianę procedur konserwacji przez wiele firm, dzięki czemu laki są skuteczniej usuwane przed wymianą oleju na nowy.
„Podczas szeroko zakrojonych testów porównawczych w warunkach laboratoryjnych i eksploatacyjnych, nasze holistyczne rozwiązanie VARTECH dotyczące laków okazało się niezwykle skuteczne w usuwaniu osadów i zapobieganiu ich powstawaniu dzięki olejom turbinowym GST Advantage. W ten sposób zyskujemy większą czystość i kontrolę nad osadami w układzie, co pomaga wydłużyć trwałość oleju i usprawnić działanie turbin.”